PERFORMANCE OF KAPOK FIBER REINFORCED POLYVINYL ALCOHOL BICOMPOSITE BY ALKALI TREATED
DOI:
https://doi.org/10.51200/bsj.v40i1.4429Keywords:
PVA, Kapok fiber, Biocomposite, Mechanical PropertiesAbstract
Raw Kapok (Ceiba pentandra) fibre was initially washed and dried before undergoes chemical treatment. Upon dried, the kapok fibre was bleached and delignified at room temperature, in an acidic solution containing 6% of sulphuric acid and 4% hydrogen peroxide to remove hemicellulose and wax. The treated kapok was filtered and washed thoroughly with distilled water and vacuum dried at 60 oC for 10 hours. Finally, the treated kapok was converted to alpha-cellulose (α-cellulose) by alkali treatment. In this step, treated kapok was immersed in 17.5% of sodium hydroxide solution for 30 minutes at a temperature of 50 oC to remove alkali-soluble components. The obtained α-cellulose, termed as alkali-treated kapok fiber (AKTF) was filtered, washed thoroughly with distilled water until pH is neutral and vacuum dried at 60 oC for 10 hours. In this stage, a certain weight of ATKF (0%, 10%, 20%, 30%, and 40%) were mixed with a hot solution of PVA and dried at room temperature. In the mechanical test, ATKF – PVA biocomposite shows an increase in tensile strength and elastic modulus up to 30% content of kapok fibre but drop at 40% kapok loading. The result shows that both ATKF – PVA biocomposite film (30%) were having the highest mechanical properties among the others and was chosen for next characterizations. It is evidence in FTIR spectra that the composites indicate the formation of new hydrogen interaction between kapok fibre and PVA which might help to improve the mechanical properties. As for XRD analysis, the ATKF – PVA biocomposite film (30%) blend was found to be a heterogeneous as the peaks of diffractogram were overlap each other. This is supported by SEM micrograph in which ATKF – PVA biocomposite (30%) show a heterogeneous phase. Additionally, in the TGA data, ATKF – PVA biocomposite (30%) was founded less thermally stable than raw kapok and pure PVA is the least thermally stable among other samples.
References
Abdulkhani, A., Hojati, M. E., Ashori, A., Hamzeh, Y., Karimi, A. N. (2013). Preparation of Cellulose/Polyvinyl Alcohol Biocomposite Films Using1-n-butyl-3-Methylimidazolium Chloride. International Journal of Biological Macromolecules, 62, 379– 386.
Abdullah, M. A., Rahmah, A. U., Man, Z. (2010). Physicochemical and Sorption Characteristics of Malaysian Ceiba pentandra (L.) Gaertn. as a Natural Oil Sorbent. Journal Hazardous Materials, 177, 683–691.
Ahad, N., Saion, E., & Gharibshahi, E. (2012). Structural, Thermal, and Electrical Properties of PVA-Sodium Salicylate Solid Composite Polymer Electrolyte. Journal of Nanomaterials, 2012, 1–8.
Asik, J., Aziz, F. A., Idris, R. (2016). Mercerized Natural Cellulose Based-Solid Polymer Electrolyte. Borneo Science, 37(2), 48 – 60.
Bondsen, D., Mathew, A., Oksman, K. (2006). Optimization of the nanocrystal from microcrystalline celluloses by acid hydrolysis. Journal of Cellulose, 13, 171–180.
Bono, A., Ying, P.H., Farm, Y. Y., Muei, C.L., Sarbatly, R., Krishnaiah, D. (2009). Synthesis and characterization of carboxymethyl cellulose from palm kernel cake. Advances in Natural and Applied Sciences, 3, 5-11.
Brebu, M., Vasile, C. (2010). Thermal degradation of lignin – A review. Cellulose Chemistry and Technology, 44, 353–363.
Campos, E., Coimbra, P., Gil, M. H. (2013). An improved Method for Preparing Glutaraldehyde Cross-linked Chitosan–Poly(vinyl Alcohol) Microparticles. Polymer Bulletin, 70, 549 – 561.
Cho, M. J., Park, B. D. (2011). Tensile and thermal properties of nanocellulose-reinforced poly(vinyl alcohol) nanocomposites. Journal of Industrial and Engineering Chemistry, 17: 36 – 40.
Draman, S. F. S., Daik, R., Abdul Latif, F., El-Sheikh, Said. M. (2013). Characterization and Thermal Decomposition Kinetics of Kapok (Ceiba pentandra L.)–Based Cellulose, BioResources, 9(1), 8 – 23.
El-Kheir, A., A., Popescu, C., Mowafi, S., Salama, M., El-Sayed, H. (2015). Physico-chemical Properties of Keratin-polyvinyl Alcohol Composite. Fibers and Polymers, 16(3), 537 – 542.
Fengel, D., & Przyklenk, M., (1986). Studies on Kapok. Holzforschung, 40 (6), 325–330.
Gaaz, T. S., Sulong, A. B., Akhtar, M. N., Kadhum, A. A. H., Mohamad, A. B., Al-Amiery AA. (2015). Properties and Applications of Polyvinyl Alcohol, Halloysite Nanotubes and Their Nanocomposites. Molecules, 20, 22833–22847.
Hajeeassa, K. S. Hussein, M. A., Anwar, Y. Tashkandi, N., Y. and Zahra M Al-amshany. (2018). Nanocomposites containing polyvinyl alcohol and reinforced carbon-based nanofiller: A super effective biologically active material. Nano Biomedicine, 5, 1–12.
Hori, K., Flavier, M. E., Kuga, S., Lam, T. B. T., & Iiyama, K. (2000). Excellent Oil Absorbent Kapok [Ceiba pentandra (L.) Gaertn.] Fibre: Fibre Structure, Chemical Characteristics, and Application. Journal Wood Science, 46 (5), 401–404.
Jahan, Z., Niazi, M. B. K., Hägg, M.-B., & Gregersen, Ø. W. (2018). Cellulose nanocrystal/PVA nanocomposite membranes for CO2 /CH4 separation at high pressure. Journal of Membrane Science, 554, 275–281.
Jumaidin, R., Sapuan, S. M., Jawaid, M., Ishak, M. R., Sahari, J. (2017). Effect of seaweed on mechanical, thermal, and biodegradation properties of thermoplastic sugar palm starch/agar composites. International Journal of Biological Macromolecules, 99, 265 –273.
Kang, P. H., Jeun, J. P., Yeoup Chung, B. Y., Kim, J. S., & Nho, Y. C. (2007). Preparation and Characterization of Glycidyl Methacrylate (GMA) Grafted Kapok Fiber by Using Radiation Induced-grafting Technique. Journal of Industrial and Engineering Chemistry, 13, 956-958.
Kim, G. M., Asran A. S., Michler G. H., Simon P., Kim, J. S. (2008). Electrospun PVA/HAp Nanocomposites Nanofibers: Biomimetics of Mineralized Hard Tissues at a Lower Level of Complexity. Bioinspiration & Biomimetics, 3(4), 1-12.
Kobayashi, Y., Matsuo, R., & Nishiyama, M. (1977). Method for Adsorption of Oils.Japanese Patent, 52,138,081, November, 17, 1977.
Laxmeshwar, S. S., Viveka, S., Kumar, D. J. M., & Nagaraja, G. K. (2012). Preparation a Properties of Composite Films from Modified Cellulose Fiber-reinforced with PLA. Journal of International Scholarly Research Network Polymer Science, 4(1), 159-168.
Liu, J. &. Wang, F., M. (2009). Effect of Alkalization Treatment on Structure and Properties of Blended Kapok Yarn. Journal of Xi’an University Engineering Science and Technology. 23, 379-386.
Lu, J., Wang, T. and Drzal, L.T. (2008). Preparation and Properties of Microfibrillated Cellulose Polyvinyl Alcohol Composite Materials. Composites Part A: Applied Science and Manufacturing. 39, 738 – 746.
Ma, N., Liu, D., Liu, Y., & Sui, G. (2015). Extraction and Characterization of Nanocellulose from Xanthoceras Sorbifolia Husks. International Journal of Nanoscience and Nano Engineering. 2: 43-50.
Matuana, L. M., Balatinecz, J., Sodhi, R. N. S., Park, C.B. (2001). Surface characterization of esterified cellulosic fibers by XPS and FTIR Spectroscopy. Wood Science and Technology, 35, 191-201.
Mwaikambo, L. Y., & Bisanda, E. T. N. (1999). The Performance of Cotton Kapok Fabric Polyester Composites. Polymer Testing, 18 (3), 181–198.
Othman, N., Azahari, N. A., & Ismail, H. (2011). Thermal Properties of Polyvinyl Alcohol (PVOH)/Corn Starch Blend Film. Malaysian Polymer Journal, 6, 147–154.
Prachayawarakorn, J., Chaiwatyothin, S., Mueangta, S., Hanchana, A. (2013). Effect of jute and kapok fibres on properties of thermoplastic cassava starch composites. Material & Design, 47, 309–315.
Purnawati, R., Febrianto, F., Wistara, I. N. J., Nikmatin, S., Hidayat, W., Lee, S. H., & Kim, N. H. (2018). Physical and Chemical Properties of Kapok (Ceiba pentandra) and Balsa (Ochroma pyramidale) Fibres. Wood Engineering, 46 (4). 393-401.
Puttaswamy, M., Srinikethan, G., Shetty, K. V. (2017). Biocomposite composed of PVA reinforced with cellulose microfibers isolated from biofuel industrial dissipate: Jatropha Curcus L. seed shell. Journal of Environmental Chemical Engineering, 5, 1990–1997.
Qiu, K., Netravali, A.N. (2013). A Composting Study of Membrane-Like Polyvinyl Alcohol Based Resins and Nanocomposites. Journal of Polymers and the Environment, 21, 658 –674.
Sonia, A., Dasan, K. P. (2013). Chemical, morphology and thermal evaluation of cellulose microfibers obtained from Hibiscus sabdariffa. Carbohydrate Polymers, 92, 668 – 674.
Srinivasa, P. C., Ramesh, M. N., Kumar, K. R., & Tharanathan, R. N. (2003). Properties and Sorption Studies of Chitosan-Polyvinyl Alcohol Blend Films. Carbohydrate Polymer, 53, 431–438.
Tiwari, R., Rana, S., Singh, S., Arora, A., Kaushik, R., Agrawal, W., Saxena, A. K., Nain, L. (2012). Biological delignification of paddy straw and Parthenium sp. using a novel micromycete Myrothecium roridum. Bioresource Technology, 135, 7 – 11.
Tye, Y. Y., Lee, K. T., Abdullah, W. N. W., & Leh, C.P. (2012). Potential of Ceiba pentandra (L.) Gaertn. (Kapok Fiber) as a Resource for Second Generation Bioethanol: Effect of Various Simple Pre-treatment Methods on Sugar Production. Bio resource Technology, 116, 536–539.
Wu, Y., Geng, F., Chang, P.R., Yu, J., Ma, X. (2006). Effect of Agar on the Microstructure and Performance of Potato Starch Film. Carbohydrate Polymer, 76, 299–304.
Yue, Y. (2011). A Comparative Study of Cellulose I and II and Fibres and Nanocrystals (Master Thesis, Louisiana State University). Retrieved from https://digitalcommons.lsu.edu/gradschool_theses/764/?utm_source=digitalcommons.lsu.edu%2Fgradschool_theses%2F764&utm_medium=PDF&utm_cam paign=PDFCoverPages
Performance of Kapok Fiber Reinforced Polyvinyl Alcohol Bicomposite by Alkali Treated
Zainuddin, S. Y. Z., Ahmad, I., Kargarzadeh, H., Abdullah, I., Dufrense, A. (2013). Potential of using multiscale kenaf fibers as reinforcing filler in cassava starch – kenaf biocomposites. Carbohydrate Polymers, 92, 2299 – 2305.
Zhang, X.Y., Fu, W.Y., Duan, C.T., Xiao, H., Shi, M.W., Zhao, N., & Xu, J. (2013). Super Hydrophobicity Determines the Buoyancy Performance of Kapok Fibre Aggregates. Applied Surface Science, 266, 225–229.
Zheng, Y., Wang, J., Zhu, Y., & Wang, A., (2015). Research and Application of Kapok Fibre as an Absorbing Material: A Mini Review. Journal of Environmental Sciences, 27, 1-12.
arch and Application of Kapok Fibre as an Absorbing Material: A Mini Review. Journal of Environmental Sciences, 27, 1-12.
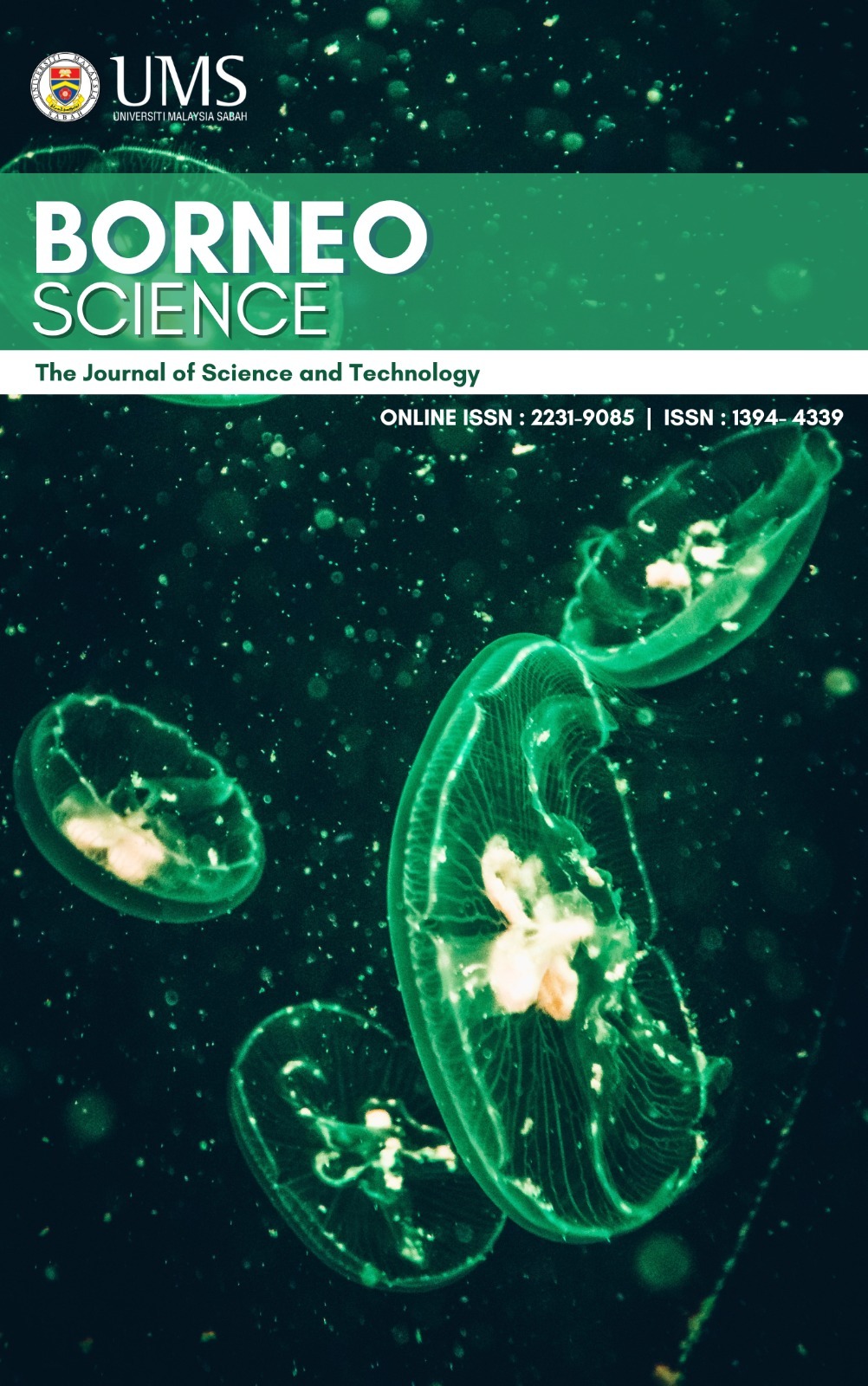
Downloads
Published
Issue
Section

