CHARACTERIZATION OF OIL PALM LEAF PAPER WITH STARCH AS BINDER
DOI:
https://doi.org/10.51200/bsj.v41i1.4445Keywords:
Agro-based pulp, Oil palm leaf paper, Soda pulping, Binding agent, Surface morphologyAbstract
The utilization of agro-based fibre in replacing the wood fibre for pulp and paper making has been the subject of interest due to the abundance of this agro-based fibre as well as to reduce the usage of wood pulp. The presence of cellulose and hemicellulose in acceptable amount for pulp paper makes this agro based fibre an alternative in paper making industry. Previous study has shown that oil palm leaf fibre can be moulded into paper sheet without any binding agent, however, the physical properties ofthe paper were very low compare to other non-wood paper. In this study, the oil palm leaf paper was prepared using 5,8,11 and 14% sodium hydroxide (NaOH) with the addition of 5% starch as the binding agent. The incorporation of starch increases the smoothness of the paper. The tear strength of the paper increases with increasing concentration of sodium hydroxide. At higher concentration ofsodium hydroxide, the paper tear index falls within the range of commercial paper tear index. This study proves that the oil palm leaf has the potential to be developed in paper making industry.
References
Aremu, M. O., Rafiu, M. A., & Adedeji, K. K. (2015). Pulp and Paper Production from Nigerian Pineapple Leaves and Corn Straw as Substitute to Wood Source. International Research
Journal of Engineering and Technology.
Asim, M., Jawaid, M., Abdan, K., & Nasir, M. (2018). Effect of Alkali treatments on physical and Mechanical strength of Pineapple leaf fibres. IOP Conference Series: Materials Science
and Engineering, 290(1). https://doi.org/10.1088/1757-899X/290/1/012030
Farsheh, A. T., Firouzabadi, M. D., & Mahdavi, S. (2011). Properties of kenaf(hibiscus cannabinus L.) bast fibre reinforced bagasse soda pulp in comparison to long fiber. World Applied
Sciences Journal, 14(6), 906–909.
Fiserova, M., Gigac, J. (2011). Comparison of hardwood kraft pulp fibre characteristics and tensile strength. Cellulose Chemicstry and Technology, 45(9–10), 627–631.
Flory., A. ., Requesens, D. V., Dvaiah, S. P., Teoh, K. T., Mansfield, S. D., & Hood, E. E. (2013). Development of green binder for paper products. BMC Biotechnology, 13(28). Retrieved from http://www.lignocellulose.ir/ojs/index.php/lignocellulose/article/view/66
Hao, E. K. Z. (2017). The Effect of Cooking Time in Paper Made from Oil Palm Leaves. Universiti Malaysia Sabah.
Hedjazi, S., Kordsachia, O., Patt, R., Latibari, A. J., & Tschirner, U. (2009). Alkaline sulfite– anthraquinone (AS/AQ) pulping of wheat straw and totally chlorine free (TCF) bleaching of pulps. Industrial Crops and Products, 29(1), 27–36. https://doi.org/10.1016/j.indcrop.2008.03.013
Khristova, P., Kordsachia, O., Patt, R., Karar, I., & Khider, T. (2006). Environmentally friendly pulping and bleaching of bagasse. Industrial Crops and Products, 23(2), 131 –139. https://doi.org/10.1016/j.indcrop.2005.05.002
Laftah, W. A., & Abdul Rahaman, W. A. W. (2015). Chemical pulping of waste pineapple leaves fiber for kraft paper production. Journal of Materials Research and Technology, 4(3), 254– 261. https://doi.org/10.1016/j.jmrt.2014.12.006
Liu, Y., Hu, T., Wu, Z., Zeng, G., Huang, D., Shen, Y., … He, Y. (2014). Study on biodegradation process of lignin by FTIR and DSC. Environmental Science and Pollution Research,
(24), 14004–14013. https://doi.org/10.1007/s11356-014-3342-5 McDonough, T. (1992). The chemistry of organosolv delignification. IPST Technical Paper Series.
Mohd Kassim, A. S., Aripin, A. M., Ishak, N., Zainulabidin, M. H., & Abang Zaidel, D. N. F. (2016). Oil palm leaf fibre and its suitability for paper-based products. ARPN Journal of
Engineering and Applied Sciences, 11(11), 7364–7369.
Rezende, C., de Lima, M., Maziero, P., deAzevedo, E., Garcia, W., & Polikarpov, I. (2011). Chemical and morphological characterization of sugarcane bagasse submitted to a delignification process for enhanced enzymatic digestibility. Biotechnology for Biofuels,
(1), 54. https://doi.org/10.1186/1754-6834-4-54 Rodríguez, A., Serrano, L., Moral, A., & Jiménez, L. (2008). Pulping of rice straw with high-boiling point organosolv solvents. Biochemical Engineering Journal, 42(3), 243–247. https://doi.org/10.1016/j.bej.2008.07.001
Rodríguez, Alejandro, Serrano, L., Moral, A., Pérez, A., & Jiménez, L. (2008). Use of high-boiling point organic solvents for pulping oil palm empty fruit bunches. Bioresource Technology,99(6), 1743–1749. https://doi.org/10.1016/j.biortech.2007.03.050
Rowell, R. M., Han, J. S., & Rowell, J. S. (2000). Characterization and Factors Effecting Fiber Properties. Natural Polymers an Agrofibers Composites, 115–134.
Saad, M. B. W., Oliveira, L. R. M., Cândido, R. G., Quintana, G., Rocha, G. J. M., & Gonçalves, A. R. (2008). Preliminary studies on fungal treatment of sugarcane straw for organosolv pulping. Enzyme and Microbial Technology, 43(2), 220–225. https://doi.org/10.1016/j.enzmictec.2008.03.006
Sahin, H. T. (2003). Base-catalyzed organosolv pulping of jute. Journal of Chemical Technology & Biotechnology, 78(12), 1267–1273. https://doi.org/10.1002/jctb.931
Soloi, S., & Hao, E. K. Z. (2019). The Potential of Oil Palm Leaf Fibre in Paper-making Industry The Potential of Oil Palm Leaf Fibre in Paper-making Industry. https://doi.org/10.1088/1742-6596/1358/1/012005
Sreekala, M. ., Kumaran, M. ., Joseph, S., & Jacob, M. (2000). Oil palm fiber reinforced phenol formaldehyde composites: Influence of fiber surface modifications on mechanical properties. Applied Composite Materials, 7(5–6), 295–329.
Ververis, C., Georghiou, K., Christodoulakis, N., Santas, P., & Santas, R. (2004). Fiber dimensions, lignin and cellulose content of various plant materials and their suitability for paper production. Industrial Crops and Products, 19(3), 245–254. https://doi.org/10.1016/j.indcrop.2003.10.006
Vu, T. H. M., Pakkanen, H., & Alén, R. (2004). Delignification of bamboo (Bambusa procera acher) Part 1. Kraft pulping and the subsequent oxygen delignification to pulp with a low kappa number. Industrial Crops and Products, 19(1). https://doi.org/10.1016/j.indcrop.2003.07.001
Wanrosli, W. D., Zainuddin, Z., Law, K. N., & Asro, R. (2007). Pulp from oil palm fronds by chemical processes. Industrial Crops and Products, 25(1), 89–94. https://doi.org/10.1016/j.indcrop.2006.07.005
Yamauchi, T., & Tanaka, A. (2002). Tearing test for paper using a tensile tester. Journal of WoodScience, 48(April 1995), 532–535. https://doi.org/10.1007/BF00766652
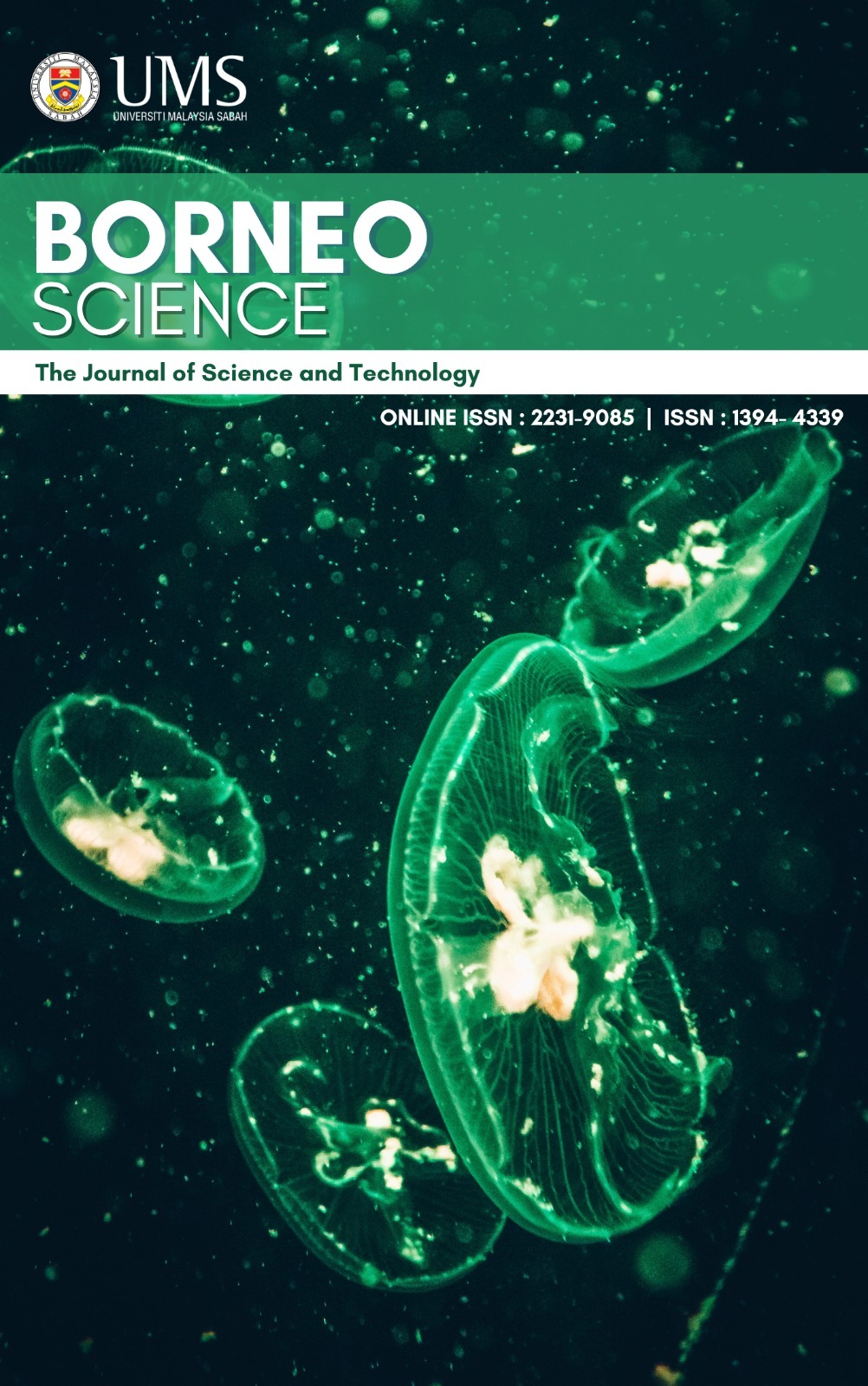
Downloads
Published
Issue
Section

